Badges, benches and candelabras in the spirit of Keizen - DIP livnica operates in line with Japanese skill principles



- When we started, our alloys were made for local metal industry but unfortunately
majority of plants stopped working – head of "DIP livnice" Branko
Jovanovic, says for eKapija.
- Smaller local market directed us towards higher placement to foreign market
so today we export over 90% produced alloy, mainly for car industry.
When it comes to countries they export to, there is Germany, Slovakia, Italy,
Slovenia and Hungary. The list of their buyers of aluminum alloy, zinc, copper
and bronze, there are still known names from Serbia or at least the ones which
used to be considered giants so today, these alloys are bought mainly by forges
which make castings for electric, textile, food and automotive industry as well
as for ship building. Thus, "Zelezara Smederevo", "Livnica
Kikinda", Indjija-based "Plamen", Aleksinac-based
"Start", Kovacica-based "Roloplast", Uzice-based
"Tekliv", "Uprim" and "Vaz" from Valjevo,"Eltex"
Krusevac, "Termovent" from Backa Topola and "Rakicevic" from
Preljina cooperate with "DIP livnica"
This Novi Sad-based forge went through Kaizen program, training in Japanese business
skill organized by SIEPA for companies in Serbia. They say they learnt a lot from
Susumu Kimura, retired head of one of Mitsubishi
firms, starting from tools labeling and work space management through cost
optimization and training of managers to motivate staff for creative participation
in work through awards and suggestions. Jovanovic says Kaizen principles became
a way of thinking of all people in forge and that they are applied today.
-The difference is visible, responsibility and discipline of all the staff who
take an active part in completion of all work tasks, maintaining and obtaining
best quality in mutual work increased – Jovanovic said.
-As a result, we are all employed and we all stood market turbulences easier as well as sudden gas price jump, metal price changes at the market and all oscillations in this business.
"DIP livnica" operates on 6.500 m2 and currently has 49 workers who
annually produce approximately 5.000 tons of alloy and the list of their
finished products comprises church bells as well. Production uses secondary raw
materials of colored metals supplied from recycling centers through purchase on
tenders, import or collectors-physical entities.
"DIP livnica" also has licenses for collection, treatment and
transport of non-hazardous waste while they collect hazardous waste and sell
it.

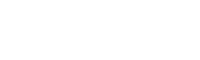


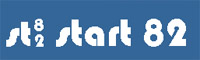
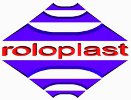
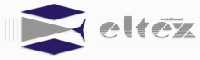
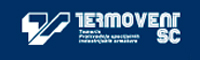
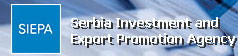
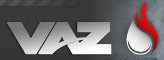